5 PPE Guidelines All Employers Should Know
1. Definition
Personal Protective Equipment (PPE) Employer Responsibilities should begin with an understanding of what it is firstly. PPE can be defined as any form of protective clothing, eyewear or headwear designed to protect the wearer from injury, ingestion or accident. PPE is designed in response to external hazards whether they be physical, chemical, airborne, electrical or heat.
2. Regulations
It is the responsibility of employers to ensure that any PPE required in the workplace is provided by the employer. In the UK employer regulations and controls are covered in the Personal Protective Equipment at Work Regulations 1992.The guiding principle of the regulations is that PPE should be used as a last resort after all precautions have been taken in a given worksite to ensure no harm will come to workers. PPE must also be assessed and maintained to make sure it is working properly and provided to employees with instructions for use. All worksites should be given a safety assessment to identify hazards that will inform the type of PPE required. Employers may need to consult specialists or manufacturers to determine the correct attire needed, e.g., in relation to chemical hazards.
3. Suitability Assessment
Assessing PPE suitability means asking questions:
- Does the PPE protect the wearer against the risks they will face?
- Does it add new risks or hazards by its restriction?
- Are different items of PPE compatible with each other?
4. Challenges and Solutions
- Head
- Falling objects, flying objects, head bumps, hair entanglement
- Hard hats, hair nets, bump caps, hoods
- Eyes
- Chemical splash, dust, projectiles, gas and vapour
- Safety spectacles, goggles, face-shields, visors
- Respiration
- Dust, vapour, gas, chemicals, low oxygen environments
- Respirators, face mask, dust mask, breathing apparatus
- Body
- Chemical or metal splash, flying objects or particles, dust, entanglement, laceration, wear and tear
- Overalls, his-vis clothing, special protective materials, aprons, chain mail
- Hands/Arms
- Lacerations, punctures, impact, chemicals, electric shock, skin reactions
- Gloves, mitts, wrist cuffs, armlets, gauntlets
- Feet/Legs
- Slips, trips, cuts and punctures, abrasion, metal or chemical splash
- Boots, wellingtons, shoes, steel toe cap, gaiters, leggings, shin protectors, aprons
- Ears
- Loud noises
- Ear defenders, earplugs
5. Training
Employers must engage with staff to train them in the necessity and use of PPE. Online safety training is a good way of ensuring training is ongoing and consistent. It makes training courses easy to deliver and easy to tailor to specific sites or jobs. Here is a handy reminder list for PPE training:
- Why – Staff must understand why PPE is essential for them
- Who – They must be made aware of who needs to wear what and when
- How – They must be trained in how to correctly identify hazards and use the correct PPE
- When – They must know that the ‘when’ of PPE is always
- Refresh – All training should be done at orientation and refreshed at regular intervals for all staff and management
Hopefully these guidelines should help you to better manage your PPE investment and better protect your workers. If you would like to learn more about online orientations or need help with building a training program for your staff then do get in touch with us here for a demo of the product.
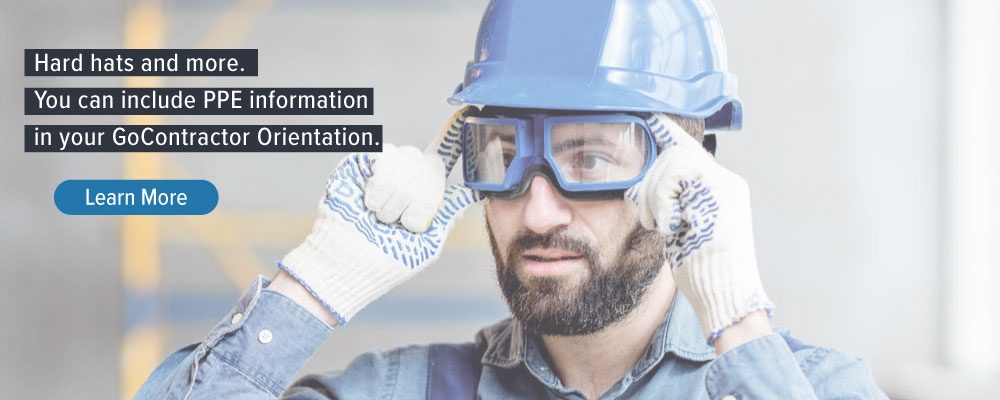