What’s your toughest job as safety manager? Getting buy-in from senior managers? Working with uncooperative supervisors? How about proving the value of your program? Whatever it is, one thing is clear: your job is challenging—and it won’t be getting easier anytime soon, not with all the OSHA regulations companies must meet daily.
But the best managers know that safety is more than rules and regulations or getting workers to abide by them. Instead, it’s about leadership and protecting workers. And about motivating them to do what they need to do. In other words, it’s about dealing effectively with human personalities in the work situation. That’s no small task.
To help you deal more effectively with workers, we’ve listed below seven habits you need to ingrain to boost your impact at work no matter what stage of your career:
1. Reinforce good behavior — Praising people is more effective than punishing them. So, praise employees verbally whenever you see them following safety procedures. You’ll boost their confidence and encourage them to keep up the good work. Also, try to get senior managers to do the same thing and to reward employees for doing a good job. Recognition from them goes a long way.
2. Lead by example — Employees often take their cue from you. If you’re lax when following safety procedures, they’ll be lax, too. If you’re diligent when following safety procedures, they’ll be diligent, too. In other words, your actions set precedence for others to follow. That’s why effective safety managers lead by example. Also, adhere to safety protocols at all times—even when no one is watching.
3. Respond quickly to issues — To be effective, you need to react to issues wherever and whenever they occur. If an employee fails to adhere to a safety regulation, you need to respond quickly and assertively. And you need to do it without compromising. Failing to do so erodes employees trust in you and the program. More important, it breeds a lax safety culture.
4. Take a proactive approach — Work on continuously to anticipate problems, especially in the area of hidden employee behaviors. You can then eliminate the risk factors before accidents occur. So, hold regular proactive consultations with employees—vital and critical resources. Also, host informal meetings to talk about high-risk areas, safety reports, proposed changes to procedures, and so on.
5. Work on continuous improvement — Focus on continuously improving and simplifying safety. Doing one thing daily drives big improvements long-term. So, remove hazards that can endanger workers before there’s an accident. Also, keep an eye on new hires. They tend to have more accidents than experienced workers. And simplify rules to make them easier to follow. It also helps assure they get done.
6. Maintain openness with employees — Tell employees when you’re going to something that affects them. Let them know when you’re monitoring things, testing alarms, bringing visitors through, or changing safety equipment procedures and why. Openness stops rumors from starting and builds trust. Workers have great interest in their environments, so give them as much of the facts as you can when conducting health or safety business in their areas.
7. Communicate. Communicate. Communicate — Maintaining good communications with workers is critical. They have a distinct advantage in highlighting hazards/issues and working as a team to eliminate them. So, stay in touch with them and talk with them often. Walk the floor regularly. And learn employees’ names, among other things. They can provide valuable input into safety rules thanks to their knowledge the workplace.
Implementing these seven habits will boost your impact as a safety leader. So, work on putting them into practice whenever and wherever you can. They’ll increase your ability to deal with human personalities more effectively. Isn’t that your most challenging job as a safety manager?
Watch the interview with Mary Darlington, a leading expert in Safety Leadership – learn how to implement safety into large scale projects and organizations.
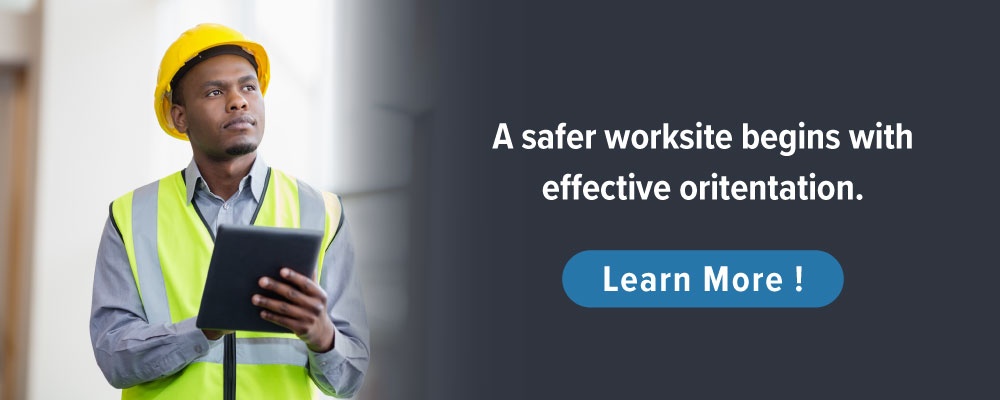