- Identify and resolve health and safety issues
- Build trust between management and workers
- Generate products and services of superior quality
- Boost worker productivity and efficiency
- Increase corporate profitability over the long-term
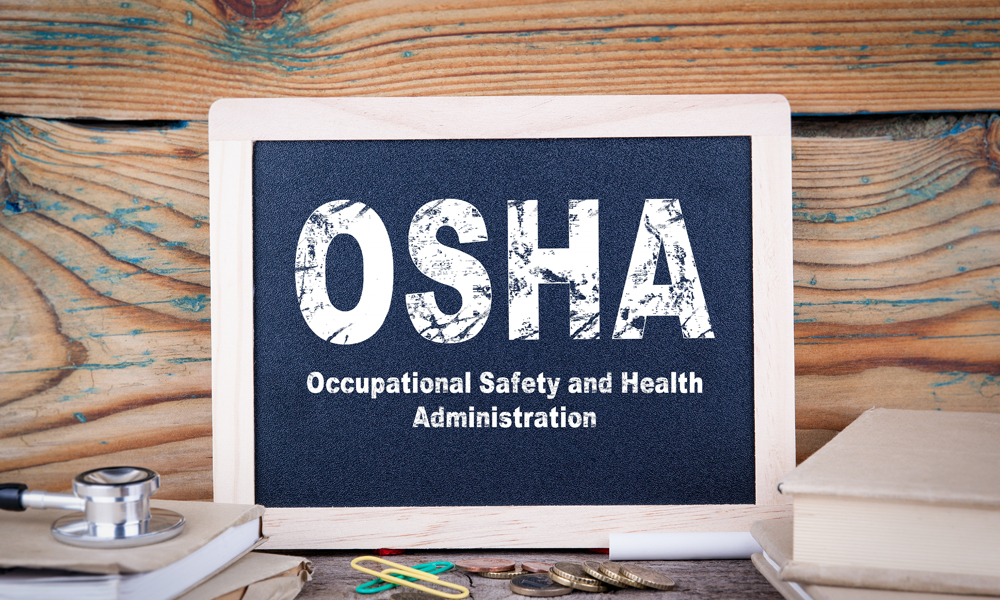
Implementing OSHA Safety Program Management Guidelines
OSHA introduced its program management guidelines in 1989. Over the years, these guidelines have provided businesses with a solid foundation and reliable plan, for creating an effective OSHA safety program. Many companies have used them to do just this, but a lot has changed in the workplace since these guidelines were first written. For example, the increased hiring of temporary and contract workers has recently formed a higher risk for businesses than ever before. Meanwhile, integrating technology into the workplace has resulted in some new and different health hazards. This is why OSHA has recently updated its guidelines, bringing them into the 21st century. OSHA’s updated guidelines:- Reflect what the agency has learned from best-in-class programs
- Place greater emphasis on involving and informing workers about it
- Provide a more dependable evaluation element
- Implement continuous program improvement
- Emphasize the need for better coordination/communication
- Build on successful methods and practices
- Meet all national/international consensus standards.
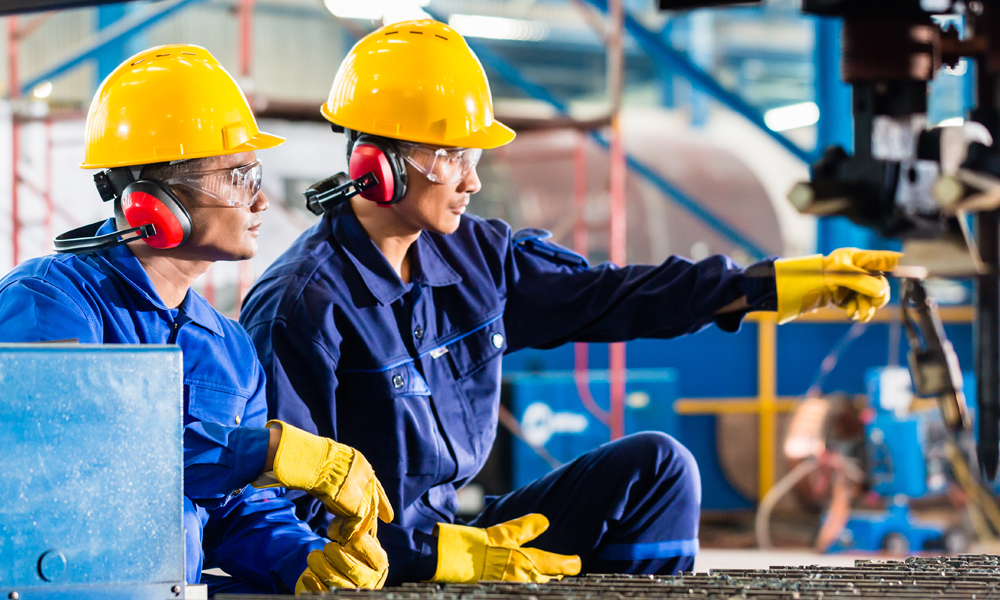
Emphasize Proactivity and Continuing Improvement
OSHA’s guidelines emphasize two things. One is a proactive approach to health and safety. It focuses on recovering and dealing with any hazards which could occur before they actually do. Put another way, proactivity forms a safer and more positive working environment, saving companies time and money, while boosting productivity and profitability. These are all good things. OSHA’s guidelines also emphasize the importance of continuous improvement. This approach starts by building a basic program that sets modest goals, monitors performance, and evaluates outcomes. Over time, you continue to improve and update programs, producing a more impressive level of worker health and safety. Using OSHA’s program management guidelines helps you to create a safety program that does everything you need it to, and more. This includes:- Improving product, service, and business process quality
- Increasing employee morale at all company work-sites
- Improving employee retention and recruitment
- Developing an impressive reputation
- Dramatically reducing compensation costs
Core Elements of OSHA’s Health and Safety Guidelines
OSHA’s guidelines cover seven core elements. These core elements are:- Management and Leadership
- Worker Participation
- Hazard Identification & Assessment
- Hazard Prevention & Control
- Education and Training
- Program Evaluation & Improvement
- Communication & Coordination
Worker Participation is a Critical Element
Worker participation is critical to meet OSHA safety programs. Workers must take part in the creation and implementation of all program elements. Much of the advice given and actions suggested in these guidelines, relies on the perspective, skills, and insights that best come from workers and their representatives. The last core element recommends any actions that the host employer can take when dealing with contractors, subcontractors, and temporary workers to ensure that everyone at the worksite is well protected. Combining these best practices using GoContractor’s platform, simplifies and streamlines this process dramatically. It also helps create a safer, more productive workplace for everyone included, an enormous benefit to any companies involved.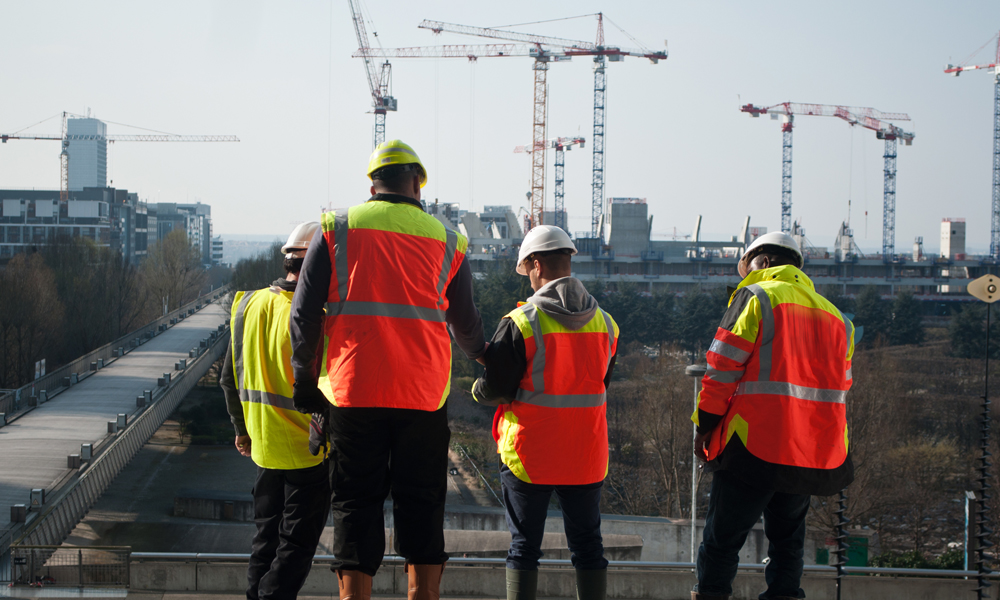
OSHA Website, Tools, and Resources
OSHA provides a website and numerous tools and resources to help you tailor its management guidelines, as well as the best methods of meeting your company requirements. You can also combine the safety program with other OSHA compliance programs, such as its Compliance Assistance Quick Start tool, delivering solid and measurable results. Workers are your most valuable assets. Without good workers, businesses wouldn’t survive for long. Protecting your workers from illness, injury or even death has to be made your top priority, if you really want to survive and thrive in today’s ever-changing business arenas. Creating an OSHA safety program based on the agency’s program management guidelines can help you do this in more a cost-effective way. Adopting the guidelines not only protects your most valuable asset but also lowers compensation costs, increasing worker uptime. Given today’s modernized workplaces and the changes that have taken place over the years, creating an OSHA safety program could be the right method of boosting productivity and profitability. This is something that every company strives for no matter what its size or the industry involved.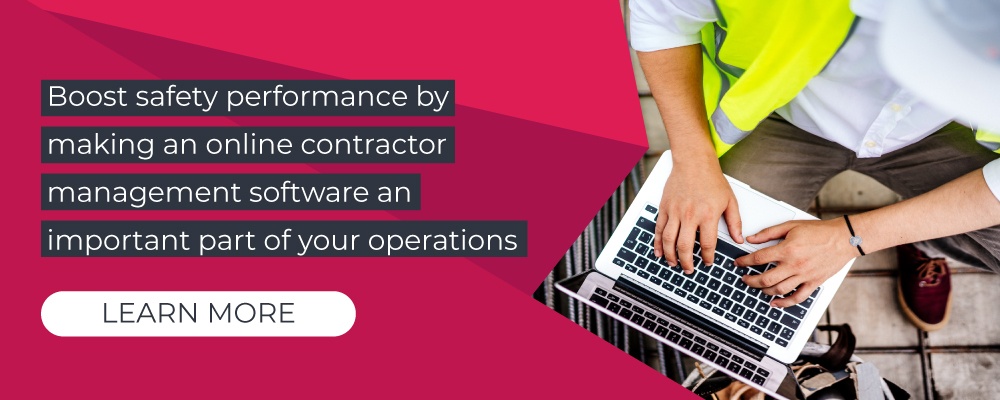