- Spending time inspiring workers with messages supporting the vision
- Using both emotional and practical messages to make a vision’s impact personal
- Providing time for people to understand and accept what safety means to them
- Using case histories to help workers understand how the vision helps them daily
- Reinforcing the messages with visual communication tools
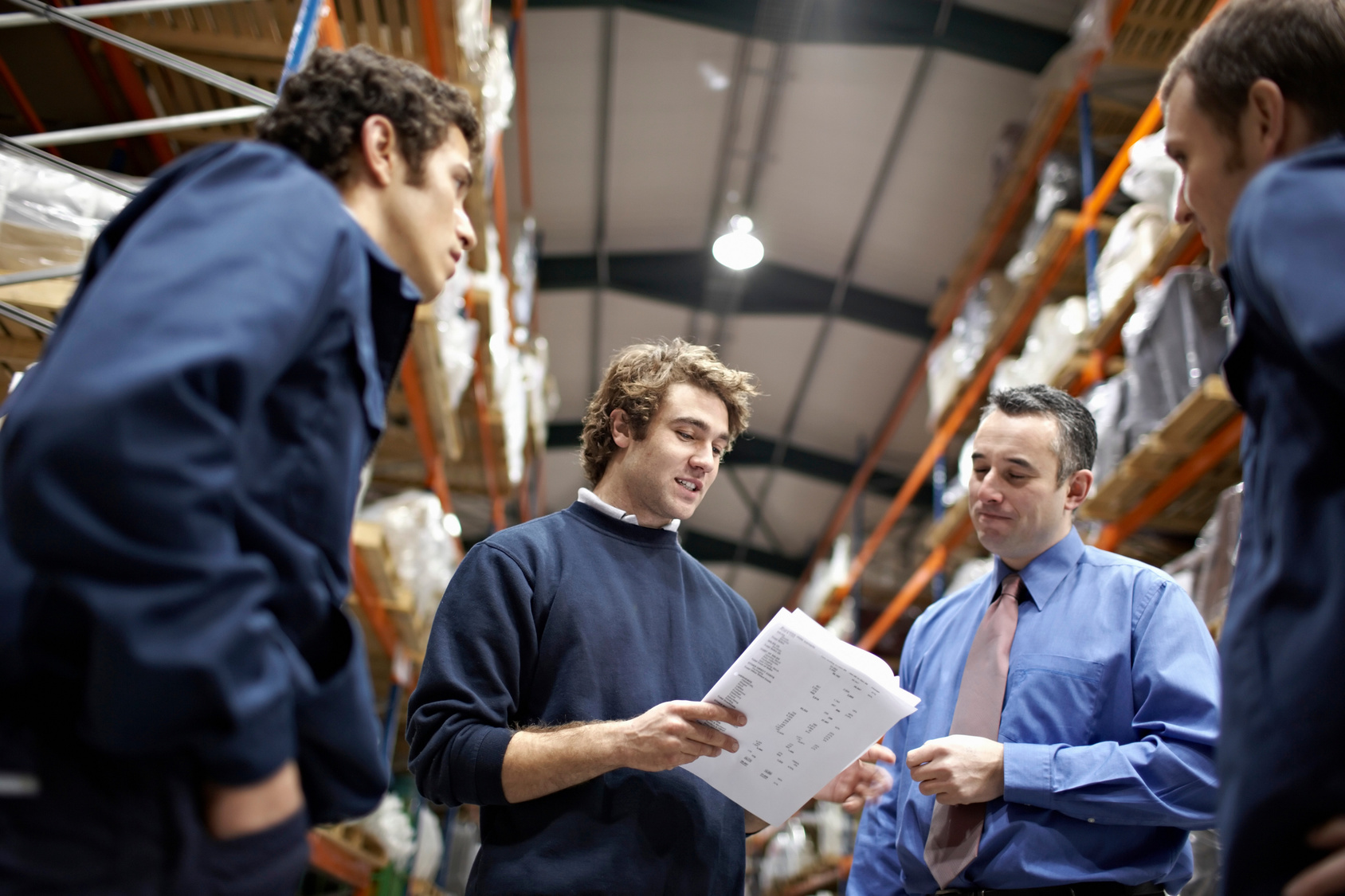
- Getting everyone to commit to safety
- Engaging workers at all levels
- Making safety an integral part of everyone’s job
- Integrating safety into the worker appraisal process
- Pre-qualify contractors for safety considerations
- Creating accountability at all levels
- Addressing safety at shift changes, weekly meetings, and job changes
- Investigating incidents and near misses to determine root causes
- Conducting regular safety inspections and audits
- Practicing caring behavior within the organization
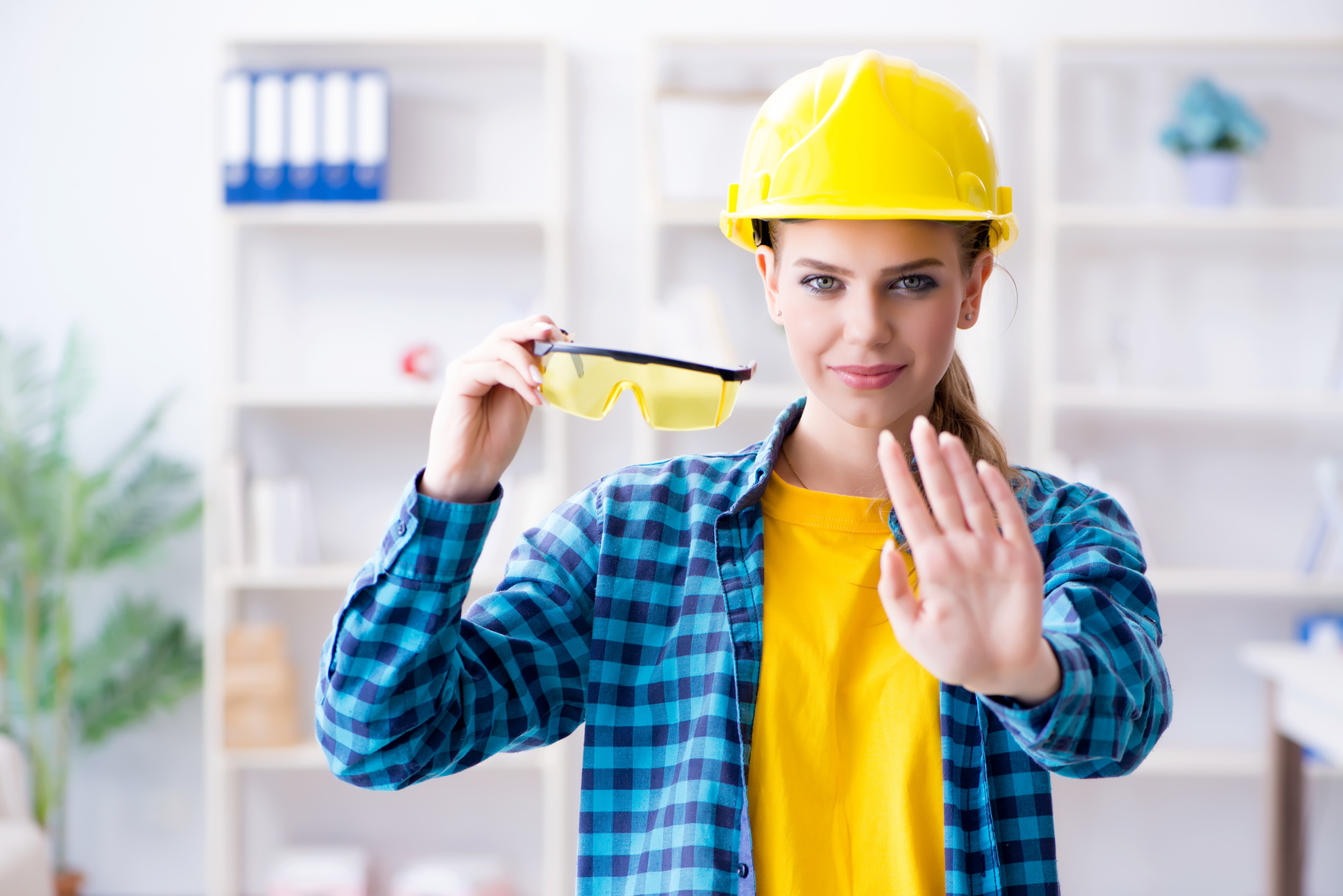
- Attitudes — Resistance to change affects the impact of every safety management system. But it’s not the only negative attitude you’ll encounter in this process. A lack of trust, a climate of fear, a leadership that won’t let go, and a history of non-employee involvement are all barriers that can derail safety at a company.
- Roles/responsibilities — Involving workers in planning and implementing a shared safety vision is great. But failing to clearly define roles and responsibilities within the safety program isn’t. Other barriers of this type include not involving key stakeholders or unions when planning, poor responses from supervisors and managers, and failing to get leadership’s full commitment.
- Training — Not providing enough time for training to occur can also block a safety culture from taking hold. Doing these things frustrates employees and creates a harmful safety atmosphere.
- Infrastructure — Systems and structures that don’t support work teams, too little or too much structure, poor communication, no transition plan, and a lack of positive recognition for all safety achievements are other barriers that can stop a shared safety vision from taking hold.
- Model good safety behavior consistently and frequently
- Ensure that management champions safety
- Train workers thoroughly and adequately
- Develop a solid transition plan
- Recognize employees for safety accomplishments
- Identify key personnel to become champions
- Create awareness of core regulatory requirements
- Define specific roles and responsibilities
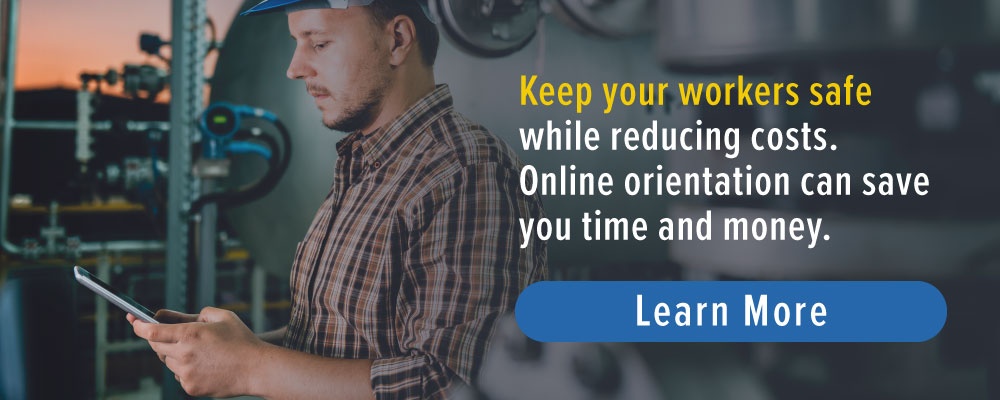