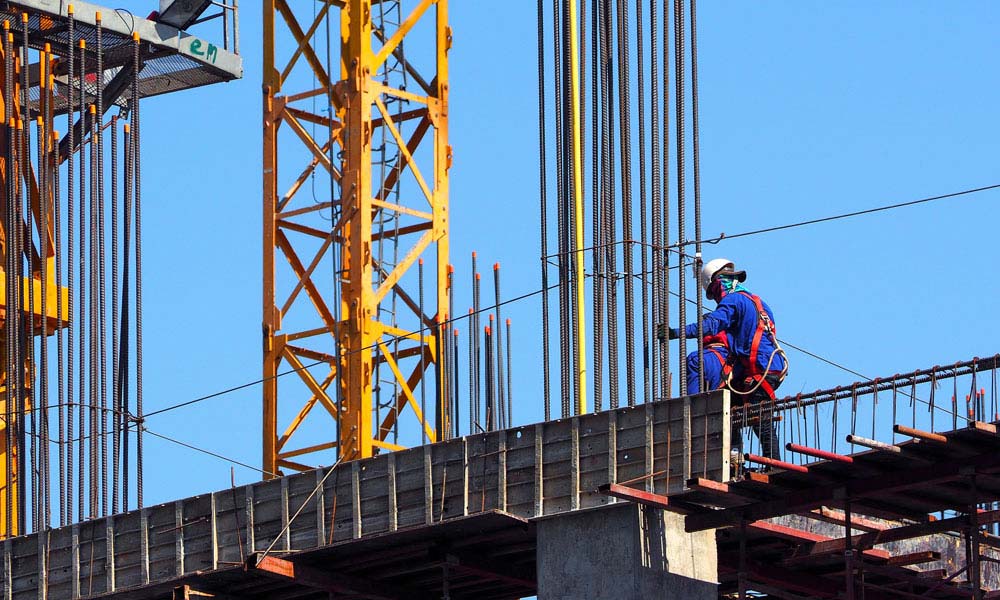
- Determine how the company’s health and safety management system operates in practice
- Identify areas where remedial action is needed
- Discover areas where a contractor safety training can be improved
- Provide a basis for continual improvement
- Provide feedback and motivation
- Where the company is relative to where they want to be
- What progress is necessary and reasonable given the circumstances
- How that progress might be achieved against particular restraints, such as resources or time
- The way progress might be achieved
- Priorities and effective use of resources.
- Suitable intervals to ensure that specific planned milestones are achieved
- Monitoring the progress with the plans is aligned with the particular timescales for achievement
- The potential for change from one state to another over time, such as during the initial design phase or whenever changes are made which could impact on the operation of the system or when information is obtained which indicates that the system as designed has failed or is flawed
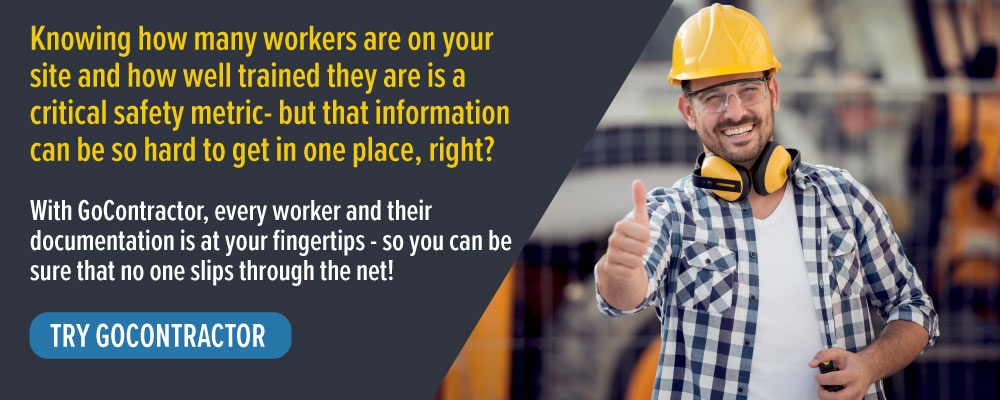