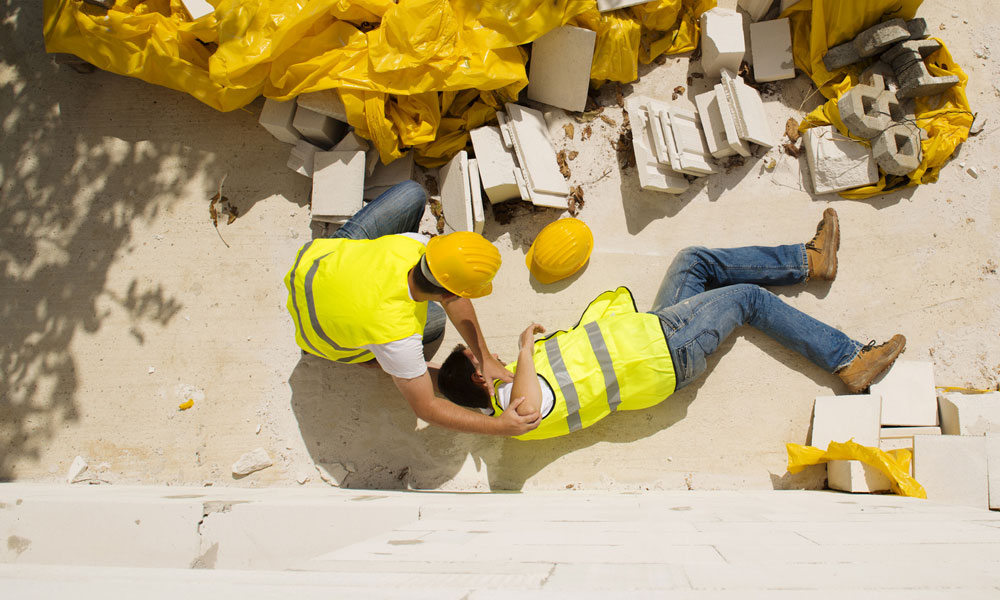
Most Common Causes of Workplace Accidents
Manual handling is a key cause of non-fatal workplace injuries in all industry sectors in Great Britain (2018). But it’s not the top cause in construction. That honor goes to slip, trips, and falls on the same working levels. That might surprise you, but it’s true. Below are the top causes of non-fatal workplace accidents in all industry sectors, according to a Health and Safety Executive report.- Slip, trip, and falls on the same level 29%
- Manual lifting and handling 22%
- Struck by object 10%
- Fall from height 8%
- Acts of violence 7%
- Contact with machinery 4%
- 82,000 workers suffered from work-related ill health
- Workers suffering from muscular-skeletal disorders 62%
- Workers suffering from depression or anxiety 25%
- Slips, falls, and trips on same level 24%
- Injured while handling, lifting, carrying 21%
- Falls from height 19%
- Struck by moving, flying, falling object 12%
- Safety Health & Welfare at Work Act 2005
- Codes of Practice/Guidelines/Other Legislation
- Safety, Health & Welfare at Work (General Application)
- Safety, Health & Welfare at Work (Construction) Regulations (2013)
Why Work Place Accidents Happen
Many workplace accidents that occur involve the person doing the work. Some experts say that as many as 80 to 100 accidents occur that way. This statistic underscores the need for you to remind workers to be more careful. Safety training helps in this regard. Below are the top six reasons why accidents involving the person doing the work happen:- Worker overconfidence — Confidence is great. But if workers enter a work site thinking nothing is going to happen to them, they’re overconfident. That’s bad news for them and you—if you’re a manager or supervisor at a construction company. Overconfidence leads to the use of improper methods, lack of proper procedures, and tool misuse.
- Poor housekeeping — The order and cleanliness of your job site reveal your attitude toward safety. Poor housekeeping and equipment disarray lead to not only unsafe working condition but also reduced productivity—especially and construction setting. Good housekeeping and tidy workplaces boost safety and productivity.
- Workplace distractions — Life’s distractions—divorces, illnesses, romantic relationships—often trigger accidents. They distract workers and have adverse effects on them and the company. Employees need to eliminate these types of distractions and focus on the job at hand to avoid workplace accidents.
- Add to these six triggers the penchant for taking job shortcuts, and you have a recipe for disaster at a work site. The last thing you need is to have an increase in the number of accidents or fatalities at your worksite or even fatality—especially if you’re in construction.
- Workplace accidents that severely injured workers can drive up your company’s costs and cut its profitability. It’s your job to prevent that from happening.
- Ignoring safety procedures — Among the worst thing a worker can do on a job site is to ignore safety protocols. Companies have safety protocols for a reason. Savvy companies educate employees on these protocols and expect them to follow them. Workers that disregard the safety protocols or fail to educate themselves on the right procedures do so at their own risk—and your company’s.
- Starting jobs while lacking information — Don’t underestimate this trigger. It happens more than you think. Make sure workers have all the information before starting a job. If you let workers start jobs without all the information, you’re asking for trouble. Having all the information also helps workers finish jobs the first time around.
- Failing to prepare for a job — Using tools like Job Safety Analysis pays off. It tells workers the best and most efficient way to do things. If your workers start tasks with hastily made plans or fail to think beforehand, they’re more likely to not only to fail at jobs but also cause accidents.Add to these six triggers the penchant for taking job shortcuts, and you have a recipe for disaster at a work site. The last thing you need is to have an increase in the number of accidents or fatalities at your worksite or even fatality—especially if you’re in construction.Workplace accidents that severely injured workers can drive up your company’s costs and cut its profitability. It’s your job to prevent that from happening.
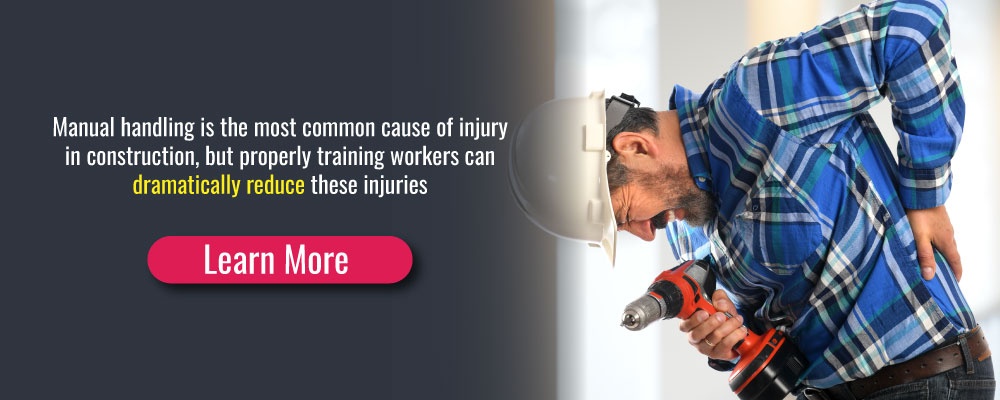