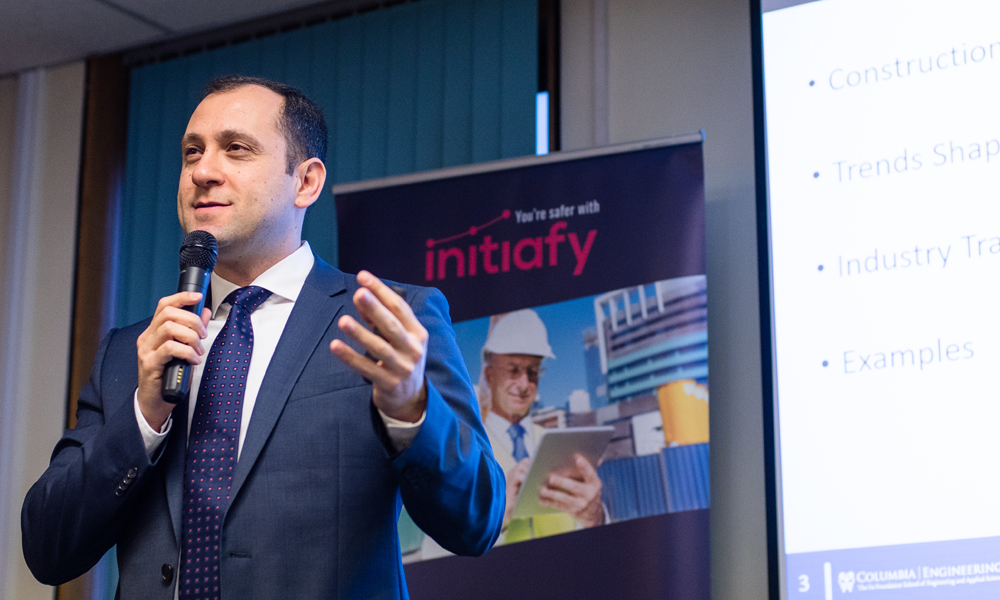
Construction Productivity Issues
Jeanette Mair pointed out key production issues in construction in a breakfast briefing held jointly by GoContractor and CIF at the agency’s Dublin offices on January 16.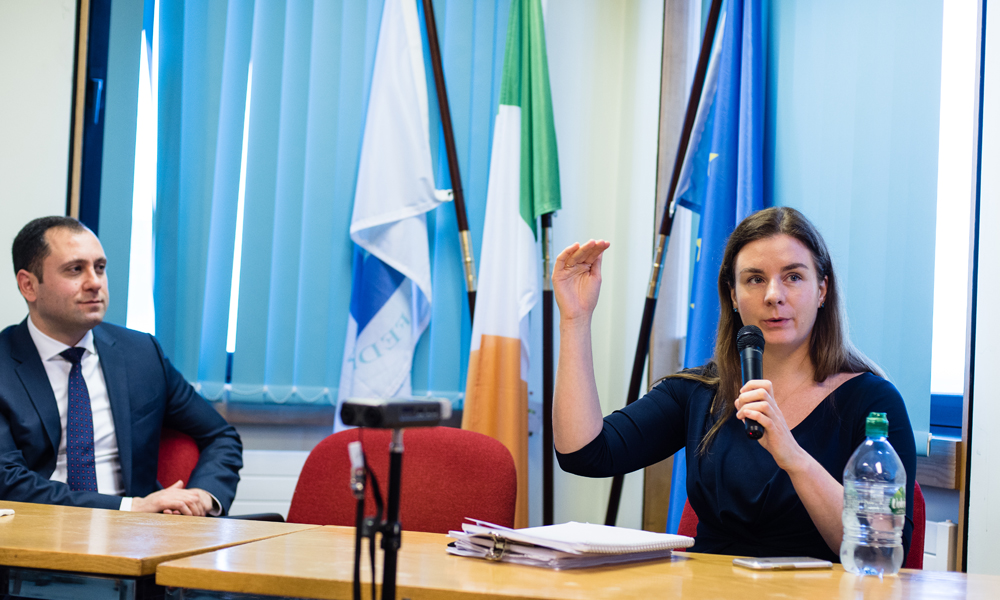
- At the industry level, she sees the key variables as the bespoke nature of the operating environment, contractual and procurement levels, and fragmented industry structure—both horizontally and vertically.
- At the firm level, she sees the critical variables as the availability of skilled labor especially at the supervisory level, underinvestment in project management basics, digitization, and innovation, and the hiring of workers to drive digitization.
- At the external level, Mair sees the key variables as increasing site and project complexities, external regulations and the cyclical nature of public investment, and problems with design processes.
Mega Trends Driving the Demand for Improvement
Professor Ibrahim Odeh also spoke at the GoContractor briefing. Odeh is Research Director and Founder of the Global Leaders in Construction Management (GLCM), Department of Civil Engineering and Engineering Mechanics at Columbia University, New York City.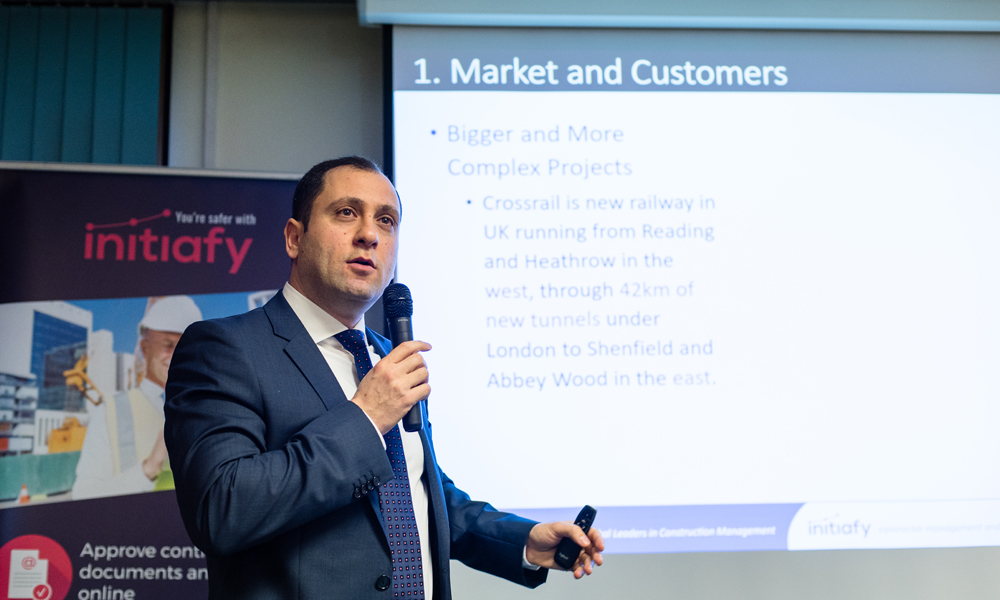
- Markets and customers
- Sustainability and resilience
- Society and workforce
- Politics and regulations
Markets and customers
Sustainability and resilience
Society and workforce
Policies and regulations
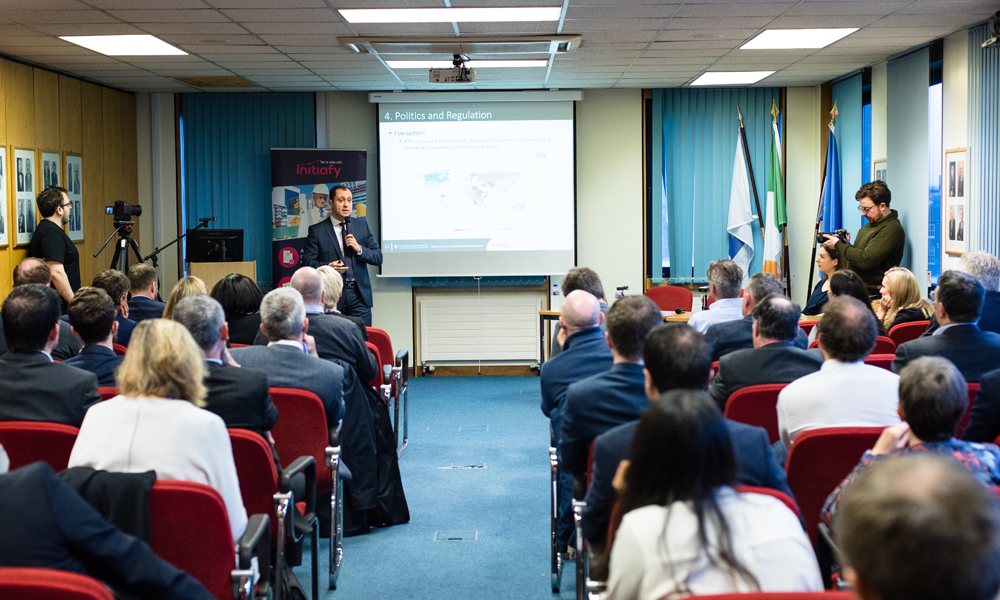
Boosting Construction Industry Productivity
Construction projects are strange business events. Minor inefficiencies in job site production can massively boost projects costs. On the other hand, incremental gains in job site production can dramatically impact on a project productivity. That can save construction companies significant time and money, boosting profitability. Below are six best practices you can implement to boost productivity at your job site and within your company:- Capitalize on technology — Adopting technology is among the best and fastest ways to enhance productivity and generate big payoffs. Solutions, like onsite productivity, project management, and building information modeling software, eliminates rework and cuts costs.
- Improve planning with more data — Analyzing the building process from end-to-end on past projects can pinpoint strengths and weaknesses in production. Implementing measures to address these areas can make a difference.
- Upgrading skills training — Boosting skills training is critical to driving up productivity on projects. Project supervisors are critical training targets. They make or break jobs.
- Increase the use of prefabrication — Prefabrication beats building from scratch almost every time. Prefabrication not only boosts productivity, but also cuts cost and enhances quality.
- Create shorter more team-friendly contracts — Instead of adding people to your legal team, create shorter contracts requiring less mediation and more engagement from team members. Japan and South Korea have done this and its paid off.
- Improve safety training and provide more of it — Worksite accidents increase project delays and cost overruns. But many construction companies use outmoded safety training practices, like classroom sessions to train workers. Technology can help here, too.
- Streamline the contractor management process
- Provide a structured roadmap for worker training
- Create a safer, more compliant workplace
- Provide workers ready to start work on the first day
- Increase training effectiveness with its online teaching approach
- Eliminate the paperwork associated with contractor management
- Enable workers to self-register their qualifications and skills online
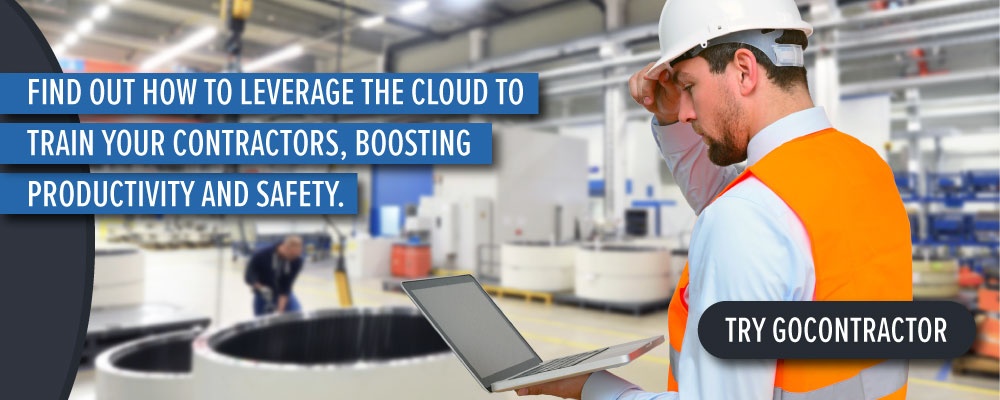